Optimize Safety with Emergency Stop Device Accessories
★Navigation bar
- What are the different types of e-stop devices?
- How can e-stop products be installed for optimal safety?
- What aspects of e-stop products require maintenance?
- What accessories can be used with e-stop products?
What are the different types of e-stop devices?
Emergency stop devices (E-Stop) are essential safety components in industrial and manufacturing fields, used to quickly stop machines or equipment in emergency situations to protect operators and equipment. Based on their design and application, e-stop devices can be divided into the following types:
1. Cable-Pull e-stop Devices: Cable-pull e-stop devices are typically installed around production lines or conveyor belts, suitable for environments requiring long-distance control. Operators can trigger the e-stop by pulling the cable, which can be pulled from any position along the production line, ensuring a quick response in emergency situations. The advantage of this device is its wide coverage, while the disadvantage is the complex installation that requires regular inspection of the cable's condition.
2. Mushroom Button e-stop Devices: Mushroom button e-stop devices are named for their mushroom-shaped head and are the most common type of e-stop device. They are usually installed on the machine's control panel, and operators can trigger the e-stop by pressing the button. The advantage of this device is its ease of operation and installation, while the disadvantage is its limited coverage area, requiring multiple buttons to cover the entire work area.
3. Foot Pedal e-stop Devices: Foot pedal e-stop devices are installed at the operator's feet and triggered by stepping on the pedal, suitable for work environments where the operator's hands are occupied. The advantage of this device is its convenient operation, especially when the operator's hands cannot leave the controls. The disadvantage is the need to ensure the operator can always reach the pedal, which requires regular inspection and maintenance of the pedal.
4. Wireless e-stop Devices: Wireless e-stop devices achieve e-stopping through wireless signal transmission, suitable for scenarios requiring remote control or mobile equipment. Operators can trigger the e-stop using a handheld device or remote control. The advantage of this device is its high flexibility, not being restricted by cable length, while the disadvantage is the need to ensure the stability of the wireless signal and the device's battery condition.
How can e-stop products be installed for optimal safety?
Installing e-stop devices is a crucial step to ensure workplace safety. To achieve optimal safety, here are some detailed installation guidelines:
1. Choose the Right Installation Location: e-stop devices should be installed in locations easily accessible to operators, ensuring quick activation in emergency situations. For example, mushroom buttons should be installed in prominent positions on control panels, and cable-pull devices should cover the entire length of the production line. The installation location should consider the operator's daily work route and standing position, ensuring they can quickly reach the e-stop device at any time.
2. Ensure Firm Installation: The installation of e-stop devices should be firm and reliable, avoiding loosening or failure due to vibration or other factors. Suitable fasteners should be used during installation, and the stability of the e-stop device should be checked regularly. For instance, the cable of a cable-pull device should be taut and not loose, and mushroom buttons should be securely fixed on the panel, without any looseness or displacement.
3. Conduct Regular Testing: After installation, regular testing of the e-stop devices should be conducted to ensure they function properly. Testing should include pressing buttons, pulling cables, and other operations to check if the device can stop the equipment promptly. Regular testing can identify and correct potential issues, ensuring the e-stop device functions correctly in critical moments.
4. Provide Clear Signage: Clear signage should be provided near e-stop devices, indicating how operators should operate in emergency situations. The signage should use conspicuous colors and clear text or icons, such as a "e-stop" sign with a red background. The signage should be checked regularly to ensure it remains clear and visible, without wear or fading.
5. Train Employees: Operators should receive training on how to use e-stop devices, understanding their location, operation methods, and precautions. Training should include practical operation drills, allowing operators to become familiar with the use of the devices.
What aspects of e-stop products require maintenance?
Regular maintenance is essential to ensure that e-stop devices function properly in critical moments. Here is a detailed guide on maintaining e-stop devices:
1. Regular Inspections: Regularly inspect the physical condition of the e-stop devices to ensure that buttons, cables, pedals, and other components are not damaged or loose. For example, check the cable of a cable-pull device for wear every month, and check the flexibility of mushroom buttons every quarter to ensure all components are in good condition.
2. Functional Testing: Conduct regular functional tests to ensure that the devices can properly stop equipment when triggered. Tests should include actual operations, such as pressing mushroom buttons or pulling cables, to check if the equipment can stop promptly. Functional tests should be conducted monthly, and test results should be recorded for reference.
3. Cleaning and Maintenance: Keep e-stop devices clean to avoid dust, grease, and other contaminants affecting their normal use. Use appropriate cleaning agents and tools, avoiding corrosive or damaging materials. For instance, wipe mushroom buttons with a clean cloth and mild cleaner, and use a soft brush to clean the cables of cable-pull devices.
4. Replacing Aging Components: Timely replace aging or damaged components to ensure the reliability and safety of the devices. For example, if the cable of a cable-pull device shows signs of wear or breakage, it should be replaced immediately. If mushroom buttons become unresponsive or loose, they should be repaired or replaced promptly.
5. Maintenance Log: Establish a maintenance log for e-stop devices, recording the dates and results of each inspection, test, and repair. A maintenance log helps track the status and history of the devices, identifying and resolving potential issues promptly.
6. Training Maintenance Personnel: Maintenance personnel should receive professional training to understand the working principles and maintenance methods of e-stop devices. Training should include both practical operations and theoretical knowledge, ensuring that maintenance personnel have the necessary skills and knowledge.
What accessories can be used with e-stop products?
The safety performance of e-stop devices can be further enhanced by pairing them with appropriate accessories. Here are some common accessories for e-stop devices and their detailed descriptions:
1. Warning Lights: Warning lights are usually installed near e-stop devices. When the e-stop is triggered, the warning lights emit a conspicuous flash to alert nearby personnel. For example, installing red flashing warning lights in a production workshop can quickly draw the attention of operators and others when an e-stop is triggered, preventing secondary accidents.
2. Alarms: Alarms emit a loud warning sound when the e-stop is triggered, further enhancing safety. Audible alarms can quickly convey emergency situations, especially in noisy environments. For instance, installing alarms in a factory workshop can produce continuous warning sounds when the e-stop is triggered, alerting all personnel to stop operations immediately and pay attention to safety.
3. Protective Covers: Installing protective covers on e-stop buttons can prevent accidental activation and increase safety. Protective covers can be transparent plastic shields that operators need to lift to press the e-stop button, avoiding unintended triggers during routine operations. For example, installing transparent protective covers on control panels can prevent tools or other objects from accidentally pressing the buttons.
4. Wireless Transmission Modules: For remote control scenarios, wireless transmission modules can be paired to achieve wireless e-stop functions. Wireless modules can be connected to e-stop devices, transmitting stop commands via wireless signals. For example, in large factories or warehouses, operators can carry wireless remote controls to trigger e-stop devices from any location.
5. Signal Converters: Signal converters can convert the trigger signals of e-stop devices into different types of signals for integration with other equipment or systems. For instance, converting mechanical signals into electrical signals facilitates connections with automation systems or remote monitoring systems, enhancing overall safety control capabilities.
6. Interlocking Devices: Interlocking devices can connect multiple e-stop devices to achieve linked control. For example, installing multiple e-stop buttons on a production line and connecting them with interlocking devices ensures that pressing any button immediately stops the entire production line, providing comprehensive safety protection.
7. Connectors: Connectors are used to link e-stop devices with other equipment or control systems. High-quality connectors ensure stable and reliable signal transmission, preventing device failures due to connection issues. For instance, our company provides connectors with waterproof and dustproof designs suitable for various harsh environments.
8. Button Boxes: Button boxes are used to install and protect e-stop buttons. They provide additional protection, preventing buttons from being damaged by external environmental factors. Button boxes should be ergonomically designed to allow operators to quickly press the button in emergencies. For example, our company's button boxes are made of high-strength materials, resistant to impact and corrosion, ensuring reliability in various environments.
By reasonably pairing these accessories, the functionality and safety performance of e-stop devices can be significantly enhanced, further ensuring workplace safety. Our company offers a variety of high-quality connectors and button boxes suitable for different e-stop devices, helping you achieve the best safety solutions.
e-stop devices and their accessories are key components in ensuring industrial safety. Whether in production workshops or automation systems, reliable e-stop devices effectively prevent accidents, protecting personnel and equipment. Choosing high-quality accessories is crucial to ensure your e-stop devices function at critical moments.
Our company not only provides various types of e-stop devices but also supplies high-quality connectors and button boxes, ensuring stable connections and easy operation of your equipment. Our products undergo rigorous quality testing, offering excellent performance and durability, suitable for various complex industrial environments. Contact us now to learn more about e-stop devices and their accessories. Let us help you create a safer, more efficient production environment. Our professional team will provide comprehensive technical support and solutions, ensuring your workplace is safe and worry-free. Visit our website or call our customer service hotline for professional consultation and product quotations. Choose us, choose safety and reliability!
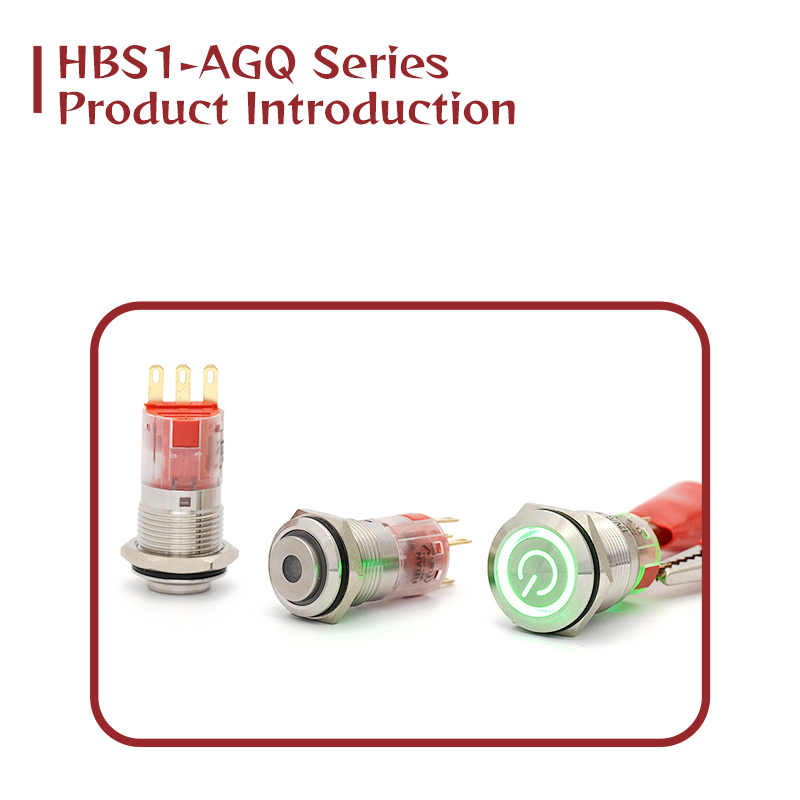
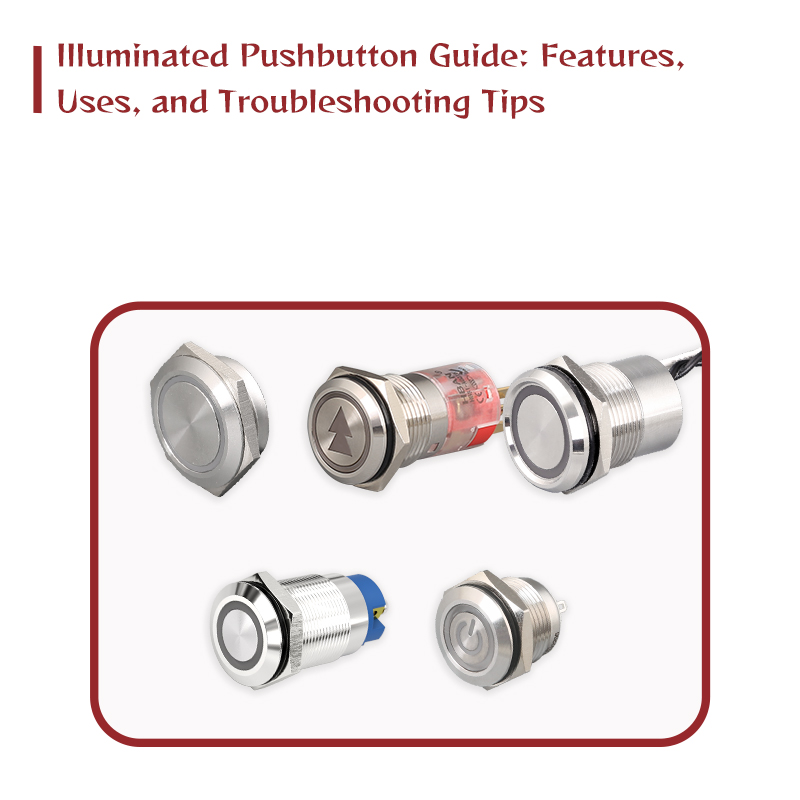

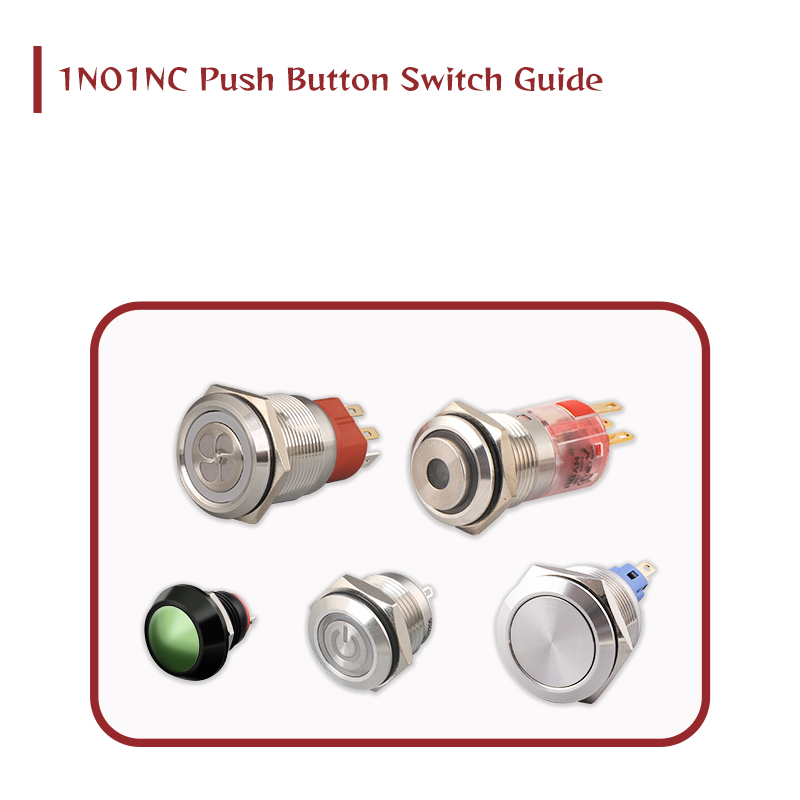
Upgrade your control system today with a reliable, space-saving